|
|
Testing PC cooling using die simulators vs. real CPUs
|
Date Posted: Dec 14 2005
|
Author: pHaestus
|
Index:
|
|
Posting Type: Article
|
Category: FAQ's, Editorials, Q&A's
|
Page: 2 of 4
|
Article Rank: from 2 Readers
Must Log In to Rank This Article
|
Forum Discussion Link
|
|
|
Testing PC cooling using die simulators vs. real CPUs By: pHaestus
|
Rationale for using a die simulator
There are some obvious advantages to using a simulator versus a real CPU. With a die simulator, it’s easy (relatively) to measure the heat load going into the system. As long as it’s properly insulated, just measure the current and voltage that you put in, characterize secondary losses, and voila! You now have the W for the popular C/W characterization of cooling performance. In fact, this C/W measurement really is driving the use of a die simulator. Strictly speaking, it’s not necessary for relative wb performance on a CPU.
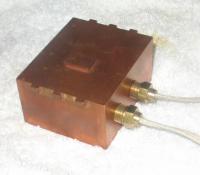
A die simulator is also fairly flexible. If you find that you need higher quality temperature readings, then you simply upgrade to better temperature probes. Motherboard Monitor CPU readings are usually limited to 1C increments but 0.01C is easily attainable with quality dual linear thermistors or RTDs. Ideally, one would expect a die simulator to have a much longer life expectancy than a real CPU. I am referring to the fact that it can survive many processor upgrade cycles and changes in brand popularity. There’s no reason that you can’t collect data on a properly maintained die simulator of the same design and spec years from now and have a huge compilation of performance that readers still find useful. However, “proper maintenance� of a die simulator is something that is extremely difficult to do. See the next section for details on this.
Die Simulator Limitations and Problems
Testing coolers with a die simulator is not without its limitations. Most of them boil down to “perhaps you aren’t simulating your CPU very well�. This isn’t actually a problem with the die simulator per se, but rather a problem with correlating the results from the simulation back to the real world.
An observation many have made is that the results that are obtained with a die simulator are strongly affected by the physical design. Specifically, the placement of temperature probes within the die simulator and the choice of die size significantly affect results. Incoherent has demonstrated (rightly I believe) that placing multiple temperature probes in a die simulator and back-calculating a “die face temperature� can address the first problem. There is no single solution to the second problem, however. Die sizes for CPUs will always change, and the introduction of integrated heat spreaders (IHS) further complicates things if you are trying to simulate them. The bottom line is that you must choose a die size when making a die-simulator, and its facial area will have a big effect on how blocks perform (small die = high heat density; large die = low heat density) on your test bed.
To elaborate on the above, a die simulator is not nearly as simple to design as one would first guess. It’s a lot more than just “a hunk of copper with a temp probe and a heater in it� and all of the dimensions and tolerances and insulation have to be done very carefully. It is not a project you can expect to do correctly without a good bit of engineering and technicall background, and it is an expensive route to go as well.
One concern of mine is that a die simulator test is unlikely to notice things that are actually important for a reviewer to spot. It is much more difficult to spot horrible mounting mechanisms, incompatibility with common motherboards, block designs that introduce lots of torque on hoses so that blocks “tip� and don’t cool well if you aren’t using a real system to test. It is also known that air coolers that provide substantial secondary path cooling to the motherboard’s other heat sources.
Another problem not often discussed in reviews using die simulator is die flatness and finish over long time periods. It is known (via Bill Adams personal correspondence) that remounting and use of the die simulator will affect the quality of its facial area. Edges and corners of the core wear away. Constant lapping and refinishing to flatness is necessary, but very few people have the resources to do this properly. Instead we get an unknown surface that is changing at every mount. Since the die simulator is presumably being designed for “high end� testing, this is actually a much more serious problem than you might first expect.
|
|
|
|
Random Forum Pic |
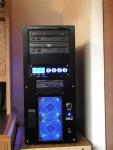 |
From Thread: Another "New guy to watercooling" thread... But I have done my homework... I think. |
| ProCooling Poll: |
So why the hell not? |
I agree!
|
67%
|
What?
|
17%
|
Hell NO!
|
0%
|
Worst Poll Ever.
|
17%
|
Total Votes:18Please Login to Vote!
|
|